Устойчивое производство графена из нефтяного кокса с использованием электрохимического расслоения
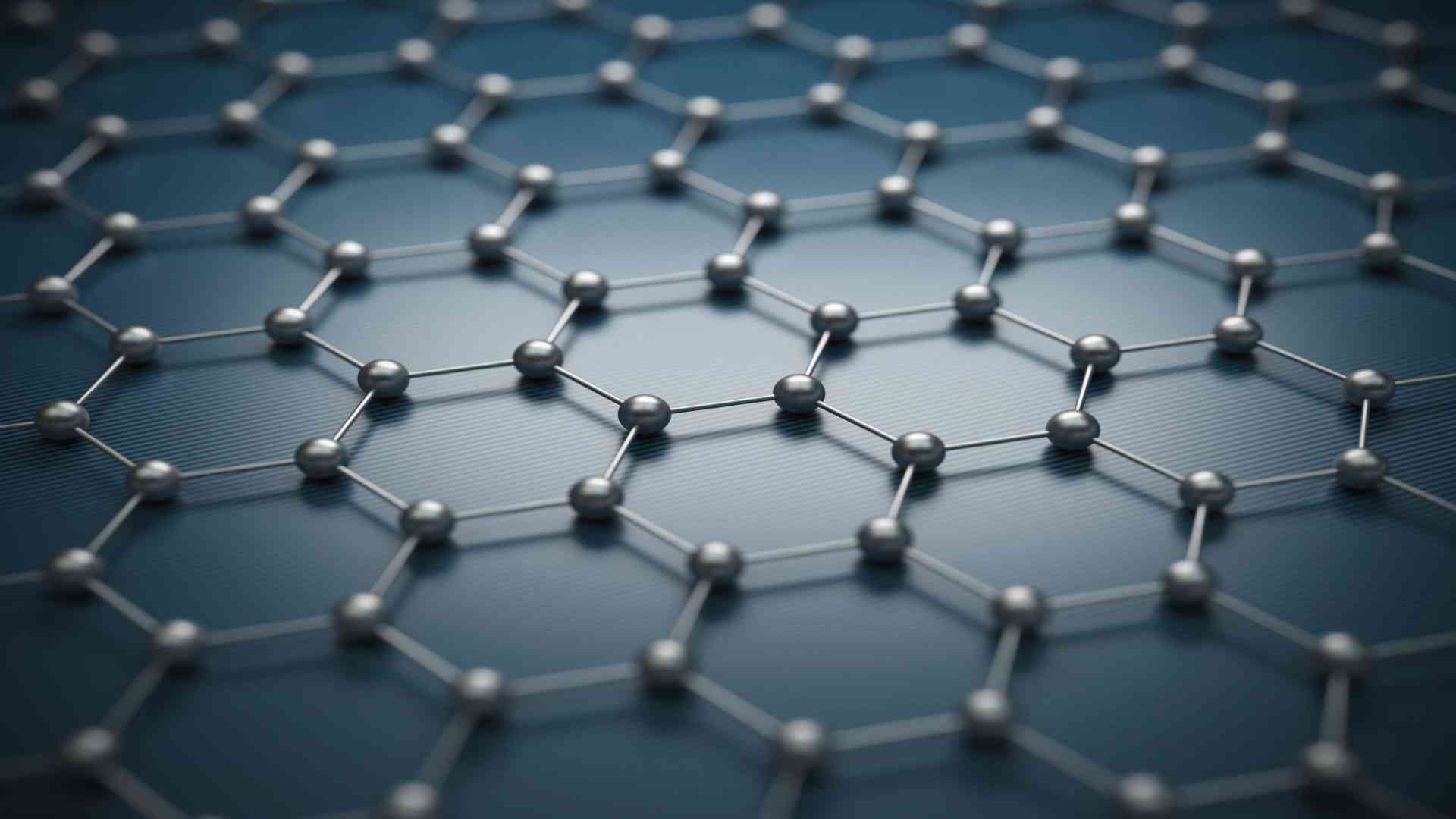
В связи с постоянным ростом озабоченности по поводу устойчивого использования ресурсов нефтехимическая промышленность сталкивается с проблемами управления каждым из своих потоков продукции. Даже побочные продукты нефтепереработки, такие как нефтяной кокс, трудно использовать рационально; кокс производится путем нагревания остатков или шламовых масел на установках нефтеперерабатывающих заводов, таких как установки жидкостного каталитического крекинга. Кокс используется в качестве топлива для отопления в нескольких отраслях промышленности, и сжигание кокса дает больше CO 2 на массу топлива, чем угля 1 . Кокс также используется в сталелитейной и алюминиевой промышленности в качестве анода для плавки, в процессе которой также выделяются парниковые газы 2 . Эти опасения подчеркивают глобальную необходимость перепрофилировать существующие нефтяные потоки, такие как кокс и его предшественники, в сторону устойчивого конечного использования
Экономика возможных процессов превращения кокса в графен весьма поразительна: игольчатый кокс, самый качественный сорт нефтяного кокса, может использоваться для производства электродов в сталелитейном производстве и может быть куплен примерно по цене 1500–3000 долларов за тонну. Массовый графеновый порошок можно приобрести в лабораторных масштабах всего за ~ 8 долларов за грамм, что на несколько порядков дороже, чем кокс. Эта последняя цена будет уменьшаться по мере увеличения масштаба, но это все равно будет на порядок увеличивать экономическую ценность.
Устойчивость агрегата зависит от межфазных свободных энергий или соответствующее межфазное натяжение поверхностей раздела твердое тело-жидкость, твердое тело-пар и жидкость-пар, которые отвечают за процесс прикрепления. Коллекторы и пенообразователи первичны реагенты, в основном контролирующие флотацию, тогда как депрессор и рН регуляторы являются вторичными, поскольку они поддерживают первичные реагенты. Графит имеет высокую естественную плавучесть, благодаря чему достигается большая плавучесть. восстановление с кинетикой первого порядка за счет многообещающего взаимодействия пенообразователя и коллектора. В общем, нефтепродукты, такие как керосин или мазута обычно используются в качестве коллектора для флотации угля по всему миру. мира.
Кроме того, нефтяной кокс является дополнительным сырьем для производства графена. Природный графит является конечным источником; по оценкам, во всем мире может быть восстановлено 800 миллионов тонн 5 . Кроме того, большая часть его трудно или непригодна для производства графена, потому что только 10–15% природного графита на самом деле представляет собой графитовый углерод; большая его часть аморфна и содержит силикатные минералы или металлы 5 . Напротив, игольчатый кокс может стабильно производиться с высоким содержанием графита и низким содержанием примесей. Мировое производство игольчатого кокса составляло 1,1 млн тонн в год по состоянию на 2020 год, и ожидается, что к 2026 году оно увеличится до 1,5 млн тонн в год 6 .. Однако эти цифры основаны на спросе на игольчатый кокс для сталелитейной промышленности и производства литий-ионных аккумуляторов; При необходимости производство игольчатого кокса может быть значительно увеличено для удовлетворения дополнительного спроса. Хотя нефть (и, следовательно, нефтяной кокс) также является ограниченным ресурсом, был достигнут прогресс в производстве игольчатого кокса из возобновляемого сырья, такого как биомасса 7 или пластиковые отходы 8 . Мало того, что игольчатый кокс может быть более постоянным сырьем для производства графена, но это также позволит нефтяному портфелю уйти от конечных потребителей с высоким уровнем выбросов.
Графен, полученный из графита, хорошо задокументирован , но графен, полученный из кокса, широко не исследовался. Предыдущие работы по производству графена из кокса в основном были сосредоточены на оксиде графена (GO) и исследовали влияние кристалличности на получающийся в результате латеральный размер. Кокс со стеариновой кислотой также изучался, но остаются вопросы о различии между исходным материалом и конечным графеноподобным продуктом, особенно в их характеристиках комбинационного рассеяния. Вероятно, это связано с отсутствием эффективных процедур разделения.
В данной работе оцениваются различные марки игольчатого кокса в качестве исходного материала для процесса ЭКО в компрессионной камере. Продукт реактора содержал непрореагировавший материал, нежелательные мелкие частицы и графеноподобный продукт, названный Coke-EEG, который был выделен методом двухэтапного центрифугирования. Морфология и состав конечного продукта подтверждают, что этот материал действительно относится к семейству графенов. Это открытие лежит в основе нового промышленного стремления к использованию природного газа и нефтяных потоков для производства ценных наноматериалов.
ЭКЭ кокса
Здесь мы показываем, что нефтяные коксы могут быть электрохимически расщеплены на графеноподобные структуры. Метод ECE зависит от интеркалирования электролита между слоями исходного материала для достижения наилучших результатов. Таким образом, более слоистый кристаллический предшественник кокса имеет больший потенциал для производства графена. Игольчатый кокс высококристаллический и имеет длинную игольчатую структуру. Высокая ароматичность и слоистая структура делают игольчатый кокс наиболее перспективным кандидатом на роль предшественника графена. Изображения, полученные с помощью сканирующего электронного микроскопа с полевой эмиссией (FE-SEM) на рис. 2 , показывают слоистую структуру CK-1 с толщиной слоя, которая может составлять меньше 100 нм
FE-SEM изображение исходного материала CK-1.а

Образец содержит как ( а) мелкие, так и ( б) относительно крупные (30–100 мкм) частицы.
На рис . 3 представлен процесс ЕСЕ, в котором исходным материалом является исходный кокс, а конечный продукт затем расслаивается и отделяется кокс (CK-d). Процесс ECE состоит из четырех этапов, подробно описанных на дополнительном рисунке 4 . Дополнительная рис. 4а описывает процесс предварительной обработки и промывки. Предварительная обработка азотной кислотой позволяет получить более гидрофильный (и смачиваемый) исходный материал, что обеспечивает лучшее воздействие раствора электролита во время процесса ЕСЕ. На дополнительном рис. 4b показан процесс разделения перед реакцией путем центрифугирования при 4000 об / мин в течение 10 мин. Отделенный исходный материал (осадок) использовался в качестве исходного материала для процесса ECE (дополнительный рис. 4c ).), который проводили при 12 В в течение 2 ч. Это напряжение необычно высокое по сравнению с напряжением, используемым для графитового ЭЭК. Однако ниже этого напряжения выход кокса-ЭЭГ довольно низок. Выше 12 В может повредиться сама мембрана. Образцы CK-b уплотнены внутри полой целлюлозной мембраны. Чтобы рабочий электрод (CK-b) оставался уплотненным в электропроводящий монолит, поверх мембраны помещается внешний груз. И рабочий, и противоэлектрод погружены в электролит. Затем при положительном смещении на рабочем электроде образцы CK-b расслаиваются до CK-c (ЭЭГ). После реакции реакционную смесь промывают и затем суспендируют в смеси этанол-вода. Продукт ECE содержал нерасслоенный кокс, более мелкий неграфитовый материал и продукт EEG.4д ; первая центрифуга удаляет непрореагировавший исходный материал, а вторая центрифуга удаляет небольшой неграфитовый материал.
Рис. 3: Схема процесса синтеза кокса и графена.

Характеристика графена, полученного из кокса
Изображения FE-SEM CK-1b и CK-1c, исходного материала и продукта процесса ECE, показаны на дополнительных рисунках 5a и дополнительных рисунках 5b соответственно. Эти изображения показывают, что процесс ECE расщепляет некоторые частицы исходного материала размером 40 мкм на более мелкие пластинчатые графеновые пластины и некоторые более мелкие неграфитовые частицы.
Что еще более важно, графеноподобные нанолисты четко видны на изображениях FE-SEM (рис. 4a, b ) CK-1d (конечный продукт, прореагировавший, а затем разделенный), что подтверждает основную гипотезу статьи. Латеральный размер листов кокса и графена значительно варьируется, причем большинство латеральных размеров находится в диапазоне 1–3 мкм. Присутствие графеновых листов было дополнительно исследовано с помощью ПЭМ. На рис . 4c , d показаны изображения CK-1d с помощью HR-TEM, на которых отчетливо видны графеноподобные листы (дополнительные изображения TEM можно найти на дополнительных рисунках 6 , 7 ). Более того, изображение с высоким разрешением показывает гексагонально упакованную кристаллическую решетку листов, как показано на рис. 4d .. Эта решетка соответствует графитовой структуре и практически идентична структуре, наблюдаемой на ЭЭГ, полученной из графита, показанной на дополнительном рисунке 8 . Листы представляют собой монокристалл, без границ зерен, наблюдаемых в поле зрения микрофотографии. (Однако листы часто содержат складки, которые потенциально могут маскировать такие особенности.) Продукт, полученный из кокса, имеет меньшую долю очень крупных частиц по сравнению с ЭЭГ, полученным из графита, вероятно, из-за тщательного разделения после обработки.
Рис. 4: Электронно-микроскопический анализ.

Сканирующая электронная микроскопия: a и b SEM-изображения CK-1d (ЭЭГ, разделенные) и c и d TEM-изображения CK-1d.
Выход графенового продукта, полученного из кокса, составил ~ 1,6%, что ниже типичных выходов ЭЭГ в 10% и более (в зависимости от условий реакции), о которых сообщалось в нашей предыдущей работе, что указывает на то, что кокс труднее расслаивается, чем графит 15 , 16 . Однако это значение намного ниже истинного выхода из-за необходимости проведения постреакции в центрифуге для выделения ЭЭГ как из исходного материала, так и из примесей. Наша предыдущая работа показывает, что значительное количество продукта графена остается в нежелательном материале и может быть восстановлено с помощью многократных проходов разделения 24 . Оставшийся материал также может быть повторно использован в процессе в качестве исходного материала без предварительной обработки.
Напротив, продукты ЕСЕ CK-2 и CK-3 не содержали значительного количества четко определенных графеноподобных листов. На дополнительном рисунке 9a показано изображение CK-3d с помощью FE-SEM. Хотя видны несколько больших листов, большая часть структур не похожа на графен, а больше похожа на большие игольчатые структуры. Кроме того, на дополнительном рисунке 9b показано изображение CK-2d с помощью FE-SEM; на этом изображении также не видны графеноподобные листы. Наличие больших пластинчатых и игольчатых структур предполагает, что графен не был успешно получен из CK-2 или CK-3 с помощью процесса ECE. ПЭМ-изображения CK-3d (дополнительный рис. 9c ) и CK-2d (дополнительный рис. 9d ).) также не имеют листообразных структур. Эти продукты ECE (CK-2d, CK-3d) сильно отличаются от графеноподобной структуры в CK-1d. Потенциальные причины этой разницы могут быть связаны со структурой исходного материала.
Нефтяной кокс производится различными способами, многие из которых являются патентованными. Хотя конкретные детали производства каждого кокса неизвестны, для определения их морфологии была проведена оптическая микроскопия каждого исходного материала. Обратите внимание, что СК-2 и СК-3 были получены в виде относительно крупных кусков и требовали шлифовки перед процессом ЕСЕ. Порошок СК-1 был очень мелким и имел значительно меньший размер частиц, чем СК-2 и СК-3. Края частиц CK-1 более зазубренные, угловатые и искаженные, тогда как частицы CK-2 и CK-3 имеют более закругленные края и не имеют слоев. Эти морфологические различия могут учитывать различия в воздействии кислоты, интеркаляции электролита и легкости отшелушивания слоя. Оптические изображения каждого исходного материала включены в дополнительные рисунки. 10 – 12. Помимо этих морфологических факторов, трехкомпонентные игольчатые коксы очень похожи, в том числе по их данным комбинационного рассеяния и ТГА (обсуждается ниже).
Электронограмма CK-1d (рис. 5а ) показывает кристаллическую структуру с хорошо упорядоченным гексагональным расположением атомов, что подтверждает образование графеноподобных нанолистов. Этот паттерн, наблюдаемый на CK-1d, аналогичен паттернам, наблюдаемым в графитовой ЭЭГ (рис. 5b ). Напротив, электронограмма исходного материала кокса СК-1 (рис. 5с ) показывает широкие (аморфные) кольца. Точно так же CK-2d (фиг. 5d ) демонстрирует аналогичные характеристики, указывающие на аморфный конечный продукт. В паттерне CK-1d есть признаки этих же признаков, что предполагает более высокое содержание аморфных элементов, чем в ЭЭГ, полученной из графита.
Рис. 5: Дифрактограммы кокса и графена, полученного из кокса.

Содержание окисления в исходном коксе и продукте ЭЭГ можно оценить несколькими способами: в нашей предыдущей работе мы показали, что термогравиметрический анализ (ТГА) можно использовать в качестве грубой меры содержания кислорода. ТГА-анализ исходного кокса и продукта ЭЭГ показан на рис. 6а . При ~700 °C половина CK-1d удаляется 15 . При той же температуре (700 °C) для CK-1a было удалено только ~10% массы, что указывает на то, что степень окисления CK-1d выше, чем CK-1a; это указывает на то, что во время ЕСЕ может происходить некоторое окисление. Однако степень окисления ниже, чем у GO или даже у графитовой ЭЭГ 15 . Рентгеновская фотоэлектронная спектроскопия (XPS) использовалась для определения состава поверхности образца CK-1d, показанного на дополнительном рисунке.С13 . Материал CK-1d имеет атомное отношение кислорода к углероду (O:C) 0,29, что остается относительно низким; кроме того, мы не наблюдали значительной связи C-O на основе подгонки пика C 1 s. Это предполагает продукт, который больше похож на графен, чем GO 25 . Элемент азота не наблюдался в этом образце, на что указывают спектры обзора XPS (ни один пик не показывает ~399 эВ, где должен быть пик N 1 s).
Рис. 6: Термогравиметрический и рамановский анализ.

Термогравиметрический анализ: ТГА СК-1а и СК-1d (инертная атмосфера). ТГА CK-1d была проведена на лиофилизированном материале, b спектры EELS, показывающие углеродный край k в CK-1a, графите, CK-1d ЭЭГ и графите ЭЭГ, и c спектры комбинационного рассеяния CK-1a, CK-1c , и CK-1d показывают разные соотношения ID/IG и характеристики двухмерных полос для исходного материала, материала после реакции ECE и после процесса центрифугирования после реакции.
Также был проведен анализ потерь энергии электронов для оценки уровня окисления. В предыдущей работе было показано, что GO имеет острый пик сразу после пика π*-возбуждения при ~279 эВ на k-крае углерода 26 . Величина этого пика увеличивается с увеличением содержания кислорода. При ~10–15% кислорода величина этого пика становится равной величине π*-пика. На рис . 6b показаны спектры, полученные от CK-1a, графита, и ЭЭГ, полученные от графита и кокса. Ни кокс, ни графит не показывают пика, соответствующего окислению. ЭЭГ, полученная из графита, содержит 10–15% кислорода, что согласуется с предыдущими выводами, тогда как ЭЭГ, полученная из кокаина, значительно меньше.
Спектры комбинационного рассеяния дают ценную информацию об углеродистых материалах. Как правило, рамановский спектр генерирует два отчетливых пика при ~1350 и 1570 см - 1 , называемых D- и G-полосами соответственно. Полоса G связана с графитовой структурой (sp 2 ), тогда как полоса D указывает на искажение или дефект (sp 3 ). В наших данных (рис. 6c ) относительная интенсивность полосы G значительно выше для CK-1d, чем для родительского CK-1 или CK-1c. Это указывает на выделение структуры sp 2 . Результаты подгонки пика комбинационного рассеяния показаны на дополнительном рисунке 14 . Кроме того, более точные значения I D /I Gотношения, основанные на интенсивности подобранных пиков D и G, также включены в дополнительный рисунок 14 .
Однако самым захватывающим открытием было появление двумерного пика в спектрах комбинационного рассеяния СК-1d (рис. 6в ).). Исходный кокс не имеет 2D-пика; это говорит о том, что в исходном коксе отсутствует достаточное количество графита, чтобы показать эту классическую характеристику графита. Небольшой двумерный горб присутствует в CK-1c, что указывает на то, что после процесса ECE присутствует значительное количество графеноподобного материала. 2D-пик еще больше (без плеча в пике) в CK-1d, подтверждая, что процесс центрифугирования отделяет графеновый продукт от нежелательного материала. Обратите внимание, что разница между этими 2D-пиками указывает на то, что наш процесс изолирует расслоенный графеноподобный материал от исходного материала, а не преобразует его; отсутствие двумерного пика в исходном коксе указывает на то, что максимально возможный выход графена будет значительно ниже, чем у графита.
Напротив, не наблюдалось существенной разницы в спектрах комбинационного рассеяния для СК-2 и СК-3 до и после эксфолиации. На дополнительном рисунке 15 показаны спектры комбинационного рассеяния CK-2a, CK-2c и CK-2d. Соотношение I D / IG у CK-2d было лишь немного ниже, чем у CK-2a и CK-2c. Однако это предполагает, что процесс ЕСЕ по-прежнему изолирует в основном структуры sp 2 даже из менее кристаллических предшественников. Аналогичный сценарий обнаружен для спектров комбинационного рассеяния CK-3a, CK-3c и CK-3d (дополнительная рис. 16 ). XRD исходных коксов (дополнительная рис. 17 ) показывает, что все исходные материалы имеют пики (002) при 26 °.
Электрические свойства и отжиг графена, полученного из кокса
Пленки вакуумной фильтрации были изготовлены из дисперсий кокса и графена, полученного из кокса. Электропроводность исходных CK-1, CK-2 и CK-3 была измерена как 0,07, 0,23 и 0,38 См / м соответственно (дополнительная таблица 1 ). Электропроводность значительно увеличилась после процесса отшелушивания и разделения; электрическая проводимость трех образцов CK-d представлена в таблице 1 . Электропроводность СК-1d высокая (~56,9 См/м), что можно объяснить его графеноподобной структурой. Однако другие образцы демонстрируют относительно низкую электропроводность. Это согласуется с результатами микроскопии, описанными ранее: CK-1d похож на графен, тогда как CK-2d и CK-3d не имеют графеноподобной морфологии.
Электропроводность графена, полученного из кокса, была ниже, чем графена, полученного из графита, поэтому на CK-1d был проведен термический отжиг (500 ° C в течение 12 часов в трубчатой печи) для увеличения его электропроводности (дополнительная таблица 2 ) . . Этот шаг значительно улучшил электропроводность как ЭЭГ, полученной из графита, так и CK-1d (дополнительная таблица 3 ) до 9735 и 250 См / м соответственно.
Дополнительное термическое восстановление и отжиг были проведены в диапазоне температур и времени для CK-1d, чтобы определить, как можно улучшить как структуру графена, так и его проводимость. Эти исследования показывают, что температура оказывает гораздо большее влияние на электропроводность, чем время (таблица 2 ). При увеличении времени отжига с 12 до 24 ч проводимость увеличилась лишь незначительно с 250 до 258 См/м (при 500 °С). Однако при повышении температуры отжига с 500 до 900 °С электропроводность значительно возрастает с 250 до 345 См/м (за 12 ч отжига). Кроме того, для отжига при 1100 °С электропроводность составляет 474 См/м. Для литий-ионных аккумуляторов требуемая проводимость составляет от 10 до 1000 См/м, так что это подходящая цель для отожженного CK-1d.27 , 28 .
Анализ потерь энергии ЭЭГ кокса, отожженного при различных температурах, не выявил различий в электронной структуре (дополнительная рис. 18 ). Одной из возможных причин повышения проводимости является удаление ковалентно связанных кислородных групп или адсорбированных примесей. Однако это должно быть достигнуто при 500 °С и 12 часах. При температуре выше 500 °C проводимость еще больше возрастает, возможно, из-за удаления других примесей или молекулярной реструктуризации 29 , 30 .. Связь между температурой и проводимостью связана с процессом реструктуризации, но этот процесс еще не до конца изучен. Обратите внимание, что улучшенная проводимость также может быть результатом улучшения контактов графен-графен в дополнение к изменению структуры графена во время отжига. Учитывая низкое исходное содержание кислорода в ЭЭГ коксового происхождения, мы заключаем, что восстановление не является основной причиной повышения проводимости. (Дополнительные данные о ТГА этих образцов можно найти во вспомогательной информации, дополнительный рисунок 19 ).
Материалы
В процессе коксования самые тяжелые компоненты нефти сжимаются паром и водой с образованием твердого нефтяного кокса. Этот процесс происходит внутри большого сосуда, называемого «установкой коксования». Сырой кокс, который выходит непосредственно из установки коксования, называется «сырым коксом» и содержит 10–20 мас.% летучих углеводородов. Нефтяные коксы делятся на три основные категории в зависимости от их применения: топливный кокс, анодный кокс и игольчатый кокс 31 , 32 .. Установка коксования может производить один из этих трех сортов в зависимости от температуры процесса, продолжительности коксования и качества углеводородного сырья. Низкосортные вакуумные остатки производят топливный кокс самого низкого качества в качестве побочного продукта с высоким содержанием примесей (тяжелые металлы, сера и азот) и используются в качестве топлива при производстве электроэнергии и в цементных печах. Относительно более качественные вакуумные отходы используются для производства анодного кокса, который имеет умеренную ценность и используется в алюминиевой промышленности. Игольчатый кокс высочайшего качества и ценности производится путем коксования высококачественного ароматического сырья, такого как декантированное масло установки жидкостного каталитического крекинга, и используется для производства высококачественных графитовых электродов для сталелитейной промышленности 29. Эти три кокса сильно различаются по своей микроскопической и макроскопической структуре. Анодный кокс имеет губчатую или сотовую морфологию, а наименее кристаллический топливный кокс состоит из агломератов сферических «дробей». Все эти коксы не имеют длительного порядка в своей структуре. Игольчатый кокс, с другой стороны, является высококристаллическим и имеет длинные игольчатые структуры. Высокая ароматичность и упорядоченная структура делают игольчатый кокс наиболее перспективным кандидатом на роль предшественника графена. Дальний порядок и ароматичность игольчатого кокса могут быть улучшены путем термической обработки 29 . Игольчатый кокс также можно графитизировать путем нагревания в инертной атмосфере при температуре >2500°C.
Для этой экспериментальной работы дихлорметан и сульфат аммония были приобретены у Sigma-Aldrich. Этанол был куплен у Fisher Chemical. В качестве исходных материалов для процесса ЕЭК использовались три различных нефтяных кокса (нефтекокс): (i) Игольчатая коксовая мелочь (СК-1), (ii) Крупные частицы игольчатого кокса (CK-2), (iii) Частицы игольчатого кокса среднего размера (CK-3) Образцы кокса модифицируются по мере прохождения процесса ЕСЕ. Для обозначения материала и стадии процесса используется система наименования: (а) Материал, который был вымыт и предварительно обработан, (b) Материал, который был отделен (до реакции), (c) Материал, подвергшийся электрохимическому расслаиванию (ЭЭГ), (d) Материал (ЭЭГ), который был центрифугирован (после реакции) и отделен от других продуктов реакции. Например, игольчатый кокс (СК-2), находящийся между стадиями разделения и реакции, обозначается как СК-2b.
Экспериментальная процедура
Процесс промывки и предварительной обработки: исходный материал промывали дихлорметаном, а затем деионизированной (ДИ) водой с помощью вакуумной фильтрации для удаления любых примесей. Затем промытый материал предварительно обрабатывали 6 М азотной кислотой, смешивая ее с материалом, используя 1 мл кислоты на грамм материала. Смесь хранили в контейнере для автоклава из нержавеющей стали и помещали в печь при температуре 120°С на 4 часа. Предварительно обработанный материал промывали деионизированной водой для нейтрализации кислоты, затем сушили в течение ночи при 100°C на плитке. Три промытых и предварительно обработанных кокса обозначены как СК-1а, СК-2а и СК-3а.
Процесс разделения перед реакцией: частицы в каждом исходном материале сильно различались по размеру. Мелкие частицы, менее пригодные для реакции, удаляли центрифугированием. Предварительно обработанный материал смешивали с водой в соотношении 5 мг/мл и центрифугировали 10 мин при 4000 об/мин. Супернатант, содержащий нежелательные более мелкие частицы, отбрасывали, а осадок собирали. Отделенные исходные коксы обозначаются как СК-1б, СК-2б и СК-3б. Эти материалы CK-b использовались в качестве исходного материала для процесса ЕСЕ.
Установка ЭКЭ и процесс реакции: предварительно обработанный и отделенный материал уплотняли в диализном мешке (длина ~ 16 см и ширина ~ 2,5 см), который был обрезан с обоих концов. Платиновая проволока была вставлена в материал в качестве рабочего электрода, а медная сетка была обернута вокруг диализного мешка в качестве противоэлектрода. Известную гирю (~0,75 кг) помещали поверх диализного мешка и медной сетки, а аппарат погружали в 2 л 0,1 М сульфата аммония ((NH4) 2 SO 4) решение. Потенциал 12 В прикладывался к платиновому электроду и медной сетке для питания процесса ЕСЕ, и реакция проводилась в течение 2 часов. После реакции продукт промывали деионизированной водой для удаления электролита. Продукт ECE содержал непрореагировавшие материалы, более мелкий неграфический материал и продукт EEG. Неразделенные продукты реакции обозначены как CK-1c, CK-2c и CK-3c.
Процесс постреакционного центрифугирования: постреакционное разделение конечного продукта проводили методом двухстадийного центрифугирования. Сначала неразделенный материал центрифугировали 10 мин при низкой скорости (2000 об/мин). На этом этапе непрореагировавшие более крупные частицы осаждали и отбрасывали, а надосадочную жидкость собирали. Во-вторых, супернатант снова центрифугировали в течение 20 мин при высокой скорости (5000 об/мин). На этом этапе из супернатанта удаляли непрореагировавшие, неграфитовые более мелкие частицы. Осадок второй стадии собирали как конечный продукт; эти отдельные коксовые ЭЭГ обозначены как CK-1d, CK-2d и CK-3d.
Процесс расчета выхода: выход графена, полученного из кокса (CK-1d), измеряли с помощью спектроскопии поглощения в УФ-видимой области с использованием коэффициента экстинкции 1293 л/г/м 33 . Измерение поглощения при 666 нм использовали для расчета концентрации ЭЭГ в дисперсии продукта. Пример спектра представлен на дополнительном рисунке 20 .
Процесс отжига: отжиг порошка CK-d проводили в трубчатой печи (Thermo Scientific Lindberg/Blue M) в атмосфере аргона. В процессе отжига образец нагревали со скоростью 10 °С/мин. СК-1d отжигали при 500 °С в течение 12 ч и 24 ч и при 900 °С и 1100 °С в течение 12 ч. Отожженные образцы были обозначены как CK-1d A1, CK-1d A2, CK-1d A3 и CK-1d A4 соответственно. После охлаждения образец порошка собирали и диспергировали в воде с помощью обработки ультразвуком в ванне. Бумага из отожженного образца была приготовлена с помощью процесса вакуумной фильтрации.
Методы характеристики
Изображение исходных коксовых материалов было выполнено на СЭМ с холодным излучением Hitachi S-4300 при ускоряющем напряжении 15 кэВ с использованием детектора вторичных электронов. Кусочки кокса наносились непосредственно на держатель образца РЭМ с помощью клейкой углеродной пленки. Кокс имел достаточную электропроводность, так что зарядки пучка не наблюдалось.
Спектры комбинационного рассеяния измеряли с использованием Horiba Jobin-Yvon LabRam HR с длиной волны лазера 633 нм, мощностью лазера 1,91 мВт, временем экспозиции 10 с и тремя накоплениями. Для удаления базовой линии использовался метод автоматической коррекции базовой линии в LabSpec.
Кривые ТГА и производной термогравиметрии (ДТГ) регистрировали с использованием прибора ТА. Для регистрации следов ТГ/ДТГ использовали скорость нагрева 10 °С/мин и размер образца 3 ± 1 мг в атмосфере N 2 (скорость потока 60 мл/мин).
Трансмиссионную электронную микроскопию проводили на трансмиссионном электронном микроскопе с холодной эмиссией JEOL F200. Кока-колу измельчали для визуализации и суспендировали в спирте. Отслоившийся материал также суспендировали в спирте. Суспензии обрабатывали ультразвуком, и каплю раствора наносили на сетку ПЭМ с ажурной углеродной опорной пленкой. Изображение было сделано при комнатной температуре с использованием ускоряющего напряжения 200 кэВ. Изображения ПЭМ и дифракционные картины записывали с помощью камеры One View in situ (Gatan, Inc.). И кокс, и расслоенный материал оказались стабильными при облучении даже при высоких дозах, необходимых для визуализации с высоким разрешением.
Спектроскопию потерь энергии проводили на трансмиссионном электронном микроскопе с холодной эмиссией JEOL F200, работающем в режиме сканирующей трансмиссионной электронной микроскопии. Для поиска образца и определения подходящего места для сбора данных использовали кольцевой детектор темного поля. Изображение спектра регистрировалось от равномерно плоской части частицы. Сбор данных осуществлялся с помощью комбинации устройства Digiscan (Gatan Inc) и Quantum GIF (Gatan Inc), работающего в режиме спектроскопии. Позже отдельные спектры из изображения спектра были суммированы, чтобы уменьшить шум, связанный со сбором данных о низкой дозе.
Химию поверхности CK-1d исследовали с использованием рентгеновского фотоэлектронного спектрометра Omicron, в котором для облучения поверхности образца использовался рентгеновский луч, полученный из источника Mg. Фотоэлектроны, испускаемые с поверхности образца, собирались полусферическим анализатором энергии электронов с углом обзора 180°. Во всех измерениях использовался угол взлета 40° между поверхностью образца и траекторией к коллектору фотоэлектронов. Во время всего сканирования выполнялась нейтрализация заряда с помощью двухлучевого нейтрализатора заряда для облучения электронов с низкой энергией для устранения сдвигов энергии связи в зарегистрированных спектрах. Образец высушивали под вакуумом в течение 24 ч для предотвращения дегазации. Спектры высокого разрешения записывали при энергии пропускания (постоянная энергия анализатора) 30,0 эВ с шагом 0,05 эВ.
Электропроводность измеряли на липкой бумаге, полученной путем вакуумной фильтрации (Fisher Scientific MaximaDry), с использованием четырехточечного датчика удельного сопротивления с питанием от Keithley 2000, 6221 и двух 6514.